Summary
What do you do? Describe your company.
Niklaus LNI SA is a Swiss manufacturing entity with 2 main divisions: chemical treatment subcontractor for the aerospace sector (Niklaus); and manufacturer of accessories for the luxury industry (MHA). The company is ISO 9001, 13485 (medical equipment) and NADCAP (chemical processes for aerospace parts) certified.
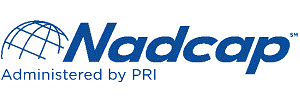
Challenge
What was your problem, and what challenges prevented you from easily solving the problem?
The company faced 2 different static quality systems, in part paper-based, poorly deployed and sub optimally used. The CEO was looking for a more engaging and dynamic quality management system for both divisions. At the same time, the organization was exploring technologies to improve communication and collaboration. The decision was made to use BPA Quality and Office 365.
How did you find out about our solution? Did you consider other providers? What criteria did you use to select BPA and Microsoft?
The company compared different solutions from many providers. They met BPA Solutions at a conference and were pleased with the product, which they found to be user-friendly and modern. As the organization was considering to acquire a product plus a collaborative technology, BPA Quality and Office 365 brought clear benefits compared to others vendors.
What was the solution? How did it address your challenges?
BPA Quality brought many benefits in the daily business. Documents are now visible to anyone, read and understood. Document versions are tracked with no paper needed anymore. Collaboration between departments has increased. Action plans are visually tracked in the solution, which allows the company to continually improve. Collaborators became engaged and active in the QMS. The management system turned to be interactive and decentralized to process owners. In the future, the company intends to go a step further and bring ERP data in BPA for better collaboration and reporting.
Strategy
How did you implement the solution? How long did it take? What new challenges did the implementation create?
The solution is intuitive and was rapidly adopted by quality managers in each division, after 5 days of BPA guidance. The tool was first introduced for the MHA division. Existing document were imported and Excel files were converted into the software.
Because of medical and aerospace specific requirements, the other division, Niklaus, implemented modules for risk management, nonconformity and continual improvement.
Results
What results did you gain from BPA Solutions – both anecdotally and measurably?
The company CEO claimed: “Quality was a concern before, but today I have no more sleepless nights thanks to the new app, and I’m not alone in carrying the management system anymore.”
“Prior implementing the app, the nonconformity handling was perceived as cumbersome by our clients. With BPA, we could reduce the time to close a nonconformity by more than 50%.
The app allows to close actions much more rapidly, which increased customer satisfaction.
The company could setup a risk management system for each process. As a benefit, It’s now much easier to discuss with process owners.”
Was there anything spectacular about how easy it was to deploy, or engage employees?
“We could achieve the NADCAP Gold –Merit level certification (the highest level) thanks in part to the software. US auditors were amazed how rapidly we could answer their questions and show proofs of evidence, live on the screen. We could demonstrate time saving in administering the QMS, spending more time improving our processes.”